PP 15L Oil Barrel Mould
Name:Paint Bucket mould
Plastic resin:PP
Mould dimension(mm):700*650*500mm
Mould weight (T):330T
Mould cavity steel:718
Mould Core steel:718
Manufacture time (day):60 Days
Mould life (ten thousand):0.3M
Cycle time:40-50s
Cooling line connector type:DME
Owing to our proficiency in this domain, we are offering our clients a wide gamut of bucket Mould. The offered mould is extensively used for designing of various kinds of buckets. Manufactured using high quality raw material and cutting-edge technology, this mould is available in different designs, shapes and sizes as per the specific requirements of clients.
About paint bucket mould, we make from 50ml to 20L with handle, for example: 100ml, 500ml,1L, 1gallon, 5L, 10L, 15L, 20L and so on. Bucket and cover mould are normally hot runner used, handle mould can be cold runner to save money. Hot runner can be chinese brand or international brand, like YUDO. For cover mould, we will make injection gate inside to let surface smooth and better for IML process.
Cavities can be one cavity for bucket and cover, handle can be 4 cavities.
For the bucket less than 1 gallon, body can be 2 cavities, cover can be 4 cavities.
About mould steel, P20, 718, H13 and 2344 are widely used. Different requirements will need different mould steel.
We could support for different testing according to project requirement, the common testing for the paint bucket samples include:
1.stacking: bucket sample could stack stable five pcs without deformation or breaking; when the lid take off, the bucket to bucket could stack well and take out easily for taper type, height should according to design requirement.
2.weight: the total weight within tolerance.
3. Water seal: put the bucket upside down for 24hours to check if any water come out or not.
PP 15L Oil Barrel Mould Design
Professional designers for your well-designed structure to achieve the shortest production cycle, to reduce unnecessary processing procedures, in order to improve production efficiency. runner structure : Cold runner, hot runner , and hot nozzle cold runner structure are the most common three.
Die accessories: insert, guide post, guide sleeve, slide, slide sets, and other wear-resistant lifter block of standard parts, in order to improve the mold life.
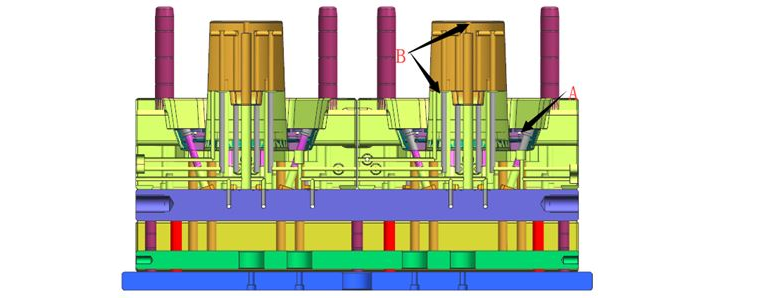
How to Choose Mould Runner?
Cold Runner:
* During the mould injection,the machine will lose more pressure and influence the life of machine.
* Because the wastage heat of the earlier material, the surface will solid. It cause the material temperature not stable and the product will have weld line,warpage,short shot and other problems.
* Some mould can not separate from gate and the plastic products automatic, low degree of automation.
* Longer cooling time,longer injection time lead to low ecomomic effectiveness
Hot Runner:
* After heating, the temperature of the injection machine barrel and the hot runner are the same. It had little pressure wastage.
* After plastic molded,the quality is good and no warpage.
* No waste material, reduce the material and cost.
* The mould had fast cooling,fast molded,improved the productivity effect.
Mould Test
Major equipment
1. CNC milling 7 sets , high-speed milling machine 1 set (precision 0.1MM)
2. EDM machine 3 sets (precision 0.1MM)
3. precision carved machine 3 sets, slope carving machine 1 set
4. drilling machine 3 sets
5. wire Cutting Machine 3 sets
6. plane grinder 1 set
7. milling machine 1 set
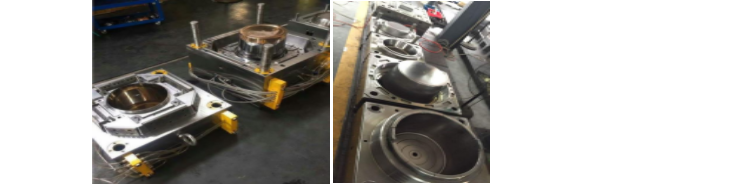
Solutions to bubble phenomenon of PP 15L Oil Barrel Mould
According to the cause of the bubble in plastic bucket mould, the solution to the problem is as follows:
1. When the wall thickness of the bucket is large, the outer surface is cooled faster than the center portion. Therefore, as the bucket moulding cooling progresses, the resin at the center portion is expanded toward the surface while being shrunk, so that the center portion is insufficiently filled. This condition is called a vacuum bubble. The main solutions are:
*Determine the proper gate and runner size based on wall thickness. Generally, the height of the gate should be 50% to 60% of the wall thickness of the plastic bucket or pails.
*A certain amount of supplementary injection material is left until the gate is sealed.
*The injection time should be slightly longer than the gate sealing time.
*Reduce the injection speed and increase the injection pressure.
*Use a material with a high melt viscosity rating.
2. The bubbles of the bucket mould caused by the generation of volatile gases are mainly solved by:
*Adequate pre-drying.
*Lower the temperature of the resin to avoid decomposition gases.
3. Bubbles caused by poor fluidity can be solved by increasing the temperature of the resin and the bucket mold and increasing the injection speed.